[ad_1]
Vietnam Textile and Garment Association (Vitas) expects the total export sales of textile and garment industry to reach about US$18.6 billion in the first six months of 2023, down 17.6% from the same period last year is equivalent to.
DIGITALIZATION HELPS REACT TO FAST DELIVERY PRESSURE
The challenges for the textile and apparel industry are the persistent global inventories, the high inflation in some key markets, the continuous rate hikes by the Fed, the negative impact of the epidemic, war and health. Buy discount…
To address these challenges, Mr. Vu Duc Giang, President of Vitas, said at the seminar “Promoting Digitization and Greening of Textile Production” organized by Vietnam Textile and Apparel Association (Vitas) and Jack Company that the Vietnamese Textile and clothing business The community, which also includes foreign direct investment companies, has adapted extremely quickly and found a way out by digitizing and greening production.
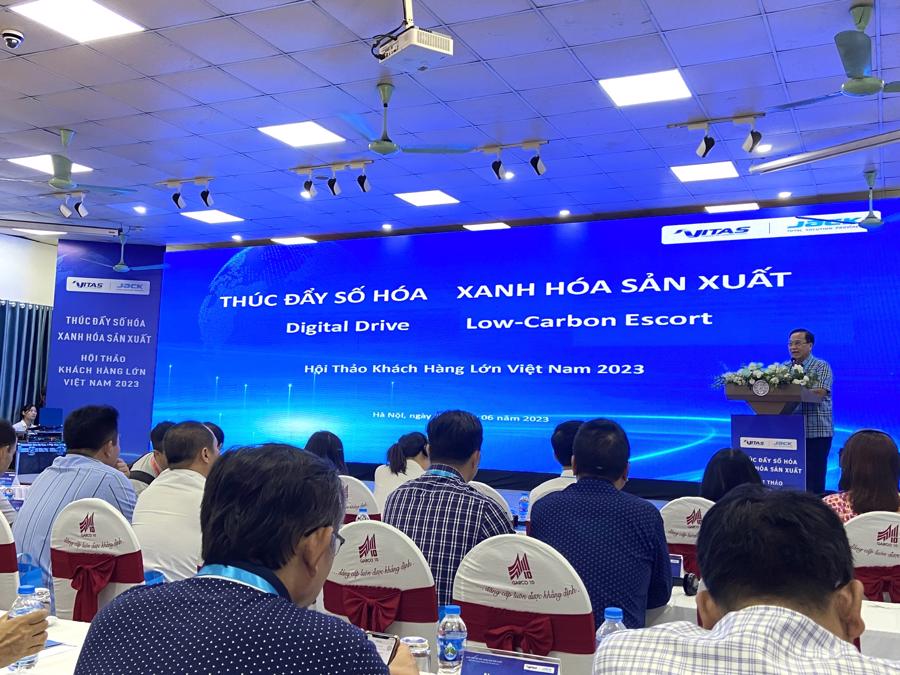
Companies have restructured their production lines, technologies, and production models to adapt from the transformation of highly specialized manufacturing to rapidly adaptable, competitive, small-volume products. Price, fast delivery, strict quality…
Mr. Zheng Haitao, general manager of Jack Technology Global Customer Strategy, said that textile and apparel companies are currently short of orders, so they need to place small orders with fast delivery. Meanwhile, customers need to submit information to know at what stage their orders are being produced, when they will be delivered, etc. Digital technology will help companies meet these demands.
Jack’s comprehensive intelligent connectivity solution with support for industrial IoT platforms and application software ecology through a series of Starlink connectivity and intelligent connectivity solutions, connecting seven “data islands” including: raw material warehouse, cutting, sewing room, final stitch, finished product warehouse, the apparel company does not not only helps to improve production efficiency, but also contributes to create a better ecological model in the industrial chain. .
In particular, the AMH (Quick Ordering King) line of machines can sew extremely thin fabrics as well as thick fabrics and stretch fabrics, helping textile companies sew hundreds of patterns a day without changing machines and adapting to different needs. New small batch clothing production process change, many styles, fast delivery.
Garment 10 Corporation pioneered the use of digitization in production stages. Garment 10 Corporation employee Trinh Duc Son said automation at many stages of production has helped workers save time. Over time, it has increased productivity by 25-30% and stabilized product quality.
Not only the automation in production, Mr. Le balancing the company’s resources; warning of the risk of bottlenecks in the production process; Quality Risk Warning.
In addition, human resources management and workforce improvement also use digital transformation to allocate jobs and calculate daily wages for employees. The data in the system is fully digitized, self-assessing the KPIs for each employee and driving the staffing plan for subordinate units to follow it according to the schedule.
TNG applies AI and uses mobile platforms to improve productivity, e.g. B. Automatic SAM calculation tool (reduces 2/3 the time of manual calculation with Excel), automatic allocation, calculation only automatic, intelligent warehouse – inventory control tool, inventory age.
GREEN IS THE WAY
The textile and apparel industry requires not only digitization and application of technology, but also greener development. Currently, many large markets such as the EU require textile products to have a long service life and be able to recycle and reuse products to reduce resource consumption, greenhouse effect and water consumption. and harmful chemicals. This is a big problem for the textile industry.
President Vitas said the government had adopted the Textile Strategy 2030-2035 – which is the backbone for the development of the industry. However, this is only a necessary but not a sufficient condition. According to Mr. Giang, we already have a textile development strategy. Now we need a specific government strategic planning strategy for solutions to develop industries, including Vietnam’s textile industry.
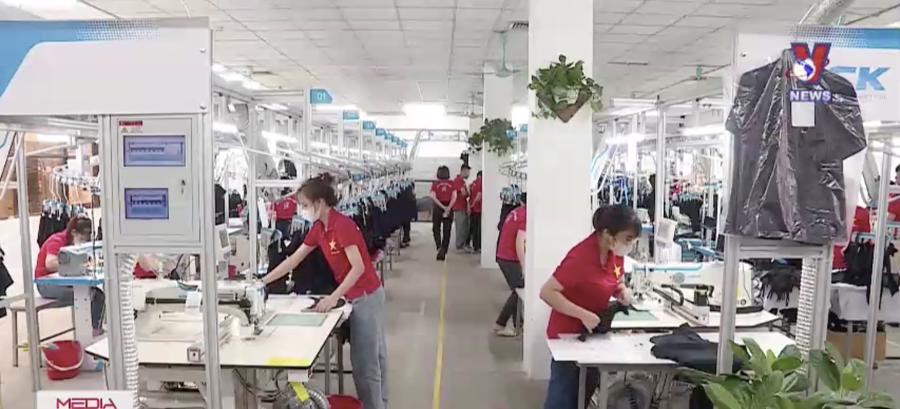
Specifically, for example, it is about the development of industrial parks to attract investments in weaving and dyeing. “Given the shortage of supplies and the need for imports, this is a major challenge. We have signed 17 Free Trade Agreements, many of which require fiber to meet requirements.
Therefore, the strategy needs to be concretely planned by the government, with the task of the place being to attract investment in weaving and dyeing… It’s not the future, but now we have to promote, we need a vision. The strategy is clearly planned,” emphasized Vitas boss.
In the vision from now to 2050, digitization and greening are inevitable trends in the textile industry. Recycling products must be adapted to textile products, this is not only mandatory on paper.
Therefore, the government must support companies to develop a greening strategy and invest in factories with infrastructure that meets brand assessment standards such as working environment, waste water, emissions and renewable energy through rooftop solar power.
In particular, there is a need to have a natural resources and environment fund to support green development and borrowing rates as low as 0-2% per annum to encourage companies to comply with COP-26 commitments. For that, the government must have cash flow strategy.
Mr. Raymond Jin, General Manager of Shengzhou Sunrise Energy, estimated Vietnam’s potential for solar energy is huge. This is an opportunity for the Vietnamese garment industry to integrate solar energy into the production system.
This is an alternative or supplemental source for the currently scarce hydroelectric power in the future, a clean, safe and infinitely usable energy source. The process of generating electricity does not pollute the environment, does not harm the ecosystem, and is also part of supporting the garment factory on the path of digital production and green production.
[ad_2]
Source link